硫化儀測得的硫化曲線怎么看?
來源:天氏庫力 發布日期
2022-07-25 瀏覽:
無轉子硫化儀測定未硫化膠料硫化特性的原理:將未硫化膠料試樣放入一個完全密封或幾乎完全密封的模腔內,并使之保持在設定的試驗溫度下。模腔有上、下兩個部分,其中一部分以微小的擺角振蕩。振蕩使試樣產生剪切應變,測定試樣對模腔的反作用轉矩(力)。此轉矩(力)取決于膠料在硫化過程中產生的、隨硫化時間長短而連續變化的剪切模量。從膠料入模開始,硫化儀便自動記錄反映膠料產生剪切應變的轉矩的數值。于是,便得到了一條轉矩與時間的關系曲線,即硫化曲線。其形狀與設定的試驗溫度和膠料的特性有關。
(有的硫化儀用FL):最小轉矩或力(N.m或N);
(有的硫化儀用Fmax):在規定時間內達到的平坦、最大、最高轉矩或力(N.m或N);
(有的硫化儀用t10):也叫焦燒時間,即轉矩達到ML+(MH-ML)*10%時所對應的時間;(有的硫化儀用t90): 也叫正硫化時間,即轉矩達到ML+(MH-ML)*90%時所對應的時間,稱為工藝正硫化時間。
硫化歷程分為四個階段:硫化誘導階段,熱硫化階段,硫化平坦階段和過硫化階段。
什么是橡膠硫化壓力?硫化壓力在橡膠成型過程中起什么作用?
橡膠件硫化的三大工藝參數是:溫度、時間和壓力。其中硫化溫度是對制品性能影響zui大的參數,硫化溫度對橡膠制品的影響的研究也比比皆是。但對硫化壓力比較少進行試驗。
硫化壓力是指,橡膠混煉膠在硫化過程中,其單位面積上所承受的壓力。一般情況下,除了一些夾布件和海綿橡膠外,其他橡膠制品在硫化時均需施加一定的壓力。
橡膠硫化壓力,是保證橡膠零件幾何尺寸、結構密度、物理機械的重要因素,同時也能保證零件表面光滑無缺陷,達到橡膠制品的密封要求。作用主要有以下幾點:
防止混煉膠在硫化成型過程中產生氣泡,提高制品的致密性;
提供膠料的充模流動的動力,使膠料在規定時間內能夠充滿整個模腔;
提高橡膠與夾件(簾布等)附著力及橡膠制品的耐曲繞性能;
4) 提高橡膠制品的物理力學性能。
硫化壓力的選取需要考慮如下幾個方面的因素:
1) 膠料的配方;
2) 膠料可塑性的大??;
3) 成型模具的結構形式(模壓,注壓,射出等);
4) 硫化設備的類型(平板硫化機,注壓硫化機,射出硫化機,真空硫化機等);
5) 制品的結構特點。
硫化壓力選取的一般原則:
1) 膠料硬度低的(50-Shore A以下或更低),壓力宜選擇小,硬度高的選擇大;
2) 薄制品選擇小,厚制品選擇大;
3) 制品結構簡單選擇小,結構復雜選擇大;
4) 力學性能要求高選擇大,要求低選擇??;
5) 硫化溫度較高時,壓力可以小一些,溫度較低時,壓力宜高點。
對硫化壓力,國內外一些橡膠廠家有如下一些經驗值供參考:
1) 模壓及移模注壓的硫化方式,其模腔內的硫化壓力為:10~20Mpa;
2) 注壓硫化方式其模腔內的硫化壓力為:0~150Mpa;
3) 硫化壓力增大,產品的靜態剛度也隨之增大,而收縮率隨之逐漸減??;(在國內的減振橡膠行業內,對于調整產品的剛度,普遍采用的依然是增加或者降低產品所使用的膠料硬度,而在國外,已經普遍采用了提高或者降低產品硫化時的膠料硫化壓力來調整產品的靜態剛度。)
4) 隨著硫化壓力的不斷提高,產品膠料的收縮率會出現一個反常的現象,即當產品膠料的硫化壓力達到83Mpa時,產品膠料的收縮率為0,若產品膠料的硫化壓力繼續不斷上升,產品膠料的收縮率會出現負值,也就是說,在這種超高的產品膠料硫化壓力下,產品硫化出來經停放后,其橡膠部分的尺寸比模具設計的尺寸還要大;
5) 在模壓和注壓方式下,模腔內膠料的硫化壓力隨著時間的延長,總是先增高后減少,并最終處于平坦狀態;
6) 隨著膠料硫化壓力的提高,其膠料的300%定伸和拉伸強度均隨之提高,其膠料的扯斷伸長率、撕裂強度和壓縮變形卻隨之下降;
7) 在減震橡膠制品硫化過程中,注壓硫化方式中模腔內膠料的壓強比模壓硫化方式的壓強高一倍以上。產品達到相同的靜剛度所需的膠料硬度有較大差別。隨產品硫化時的硫化壓力提高,產品在壓縮變形性能方面有明顯的提高。
1. 什么是硫化溫度
橡膠硫化溫度是硫化三大要素之一,是橡膠進行硫化反應(交聯反應)的基本條件,直接影響橡膠硫化速度和制品的質量。與所有化學反應一樣,硫化反應隨著溫度升高而加快,易于生成較多的低硫交聯鍵;硫化溫度低,則速度慢,生成效率低,生成較多的多硫交聯鍵。硫化溫度并且大體適用范特霍夫定律,即溫度每上升8~10℃(約相當于一個表壓的蒸汽壓力),其反應速度約增加一倍;或者說,反應時間約減少一半。
2. 怎樣選擇硫化溫度
2.1 橡膠的種類 隨著室溫硫化膠料的增加和高溫硫化的出現,硫化溫度趨向兩個。從提高硫化效率來說,應當認為硫化溫度越高越好,但實際上不能無限提高硫化溫度。橡膠為高分子聚合物,高溫會使橡膠分子鏈產生裂解反應,導致交聯鍵斷裂,即出現“硫化返原”現象,從而使硫化膠的物理機械性能下降。如高溫硫化天然橡膠時,溶于橡膠中的氧隨著溫度提高而活性加大,引起強烈的氧化作用,破壞了橡膠的組織,降低了硫化膠的物理機械性能。
綜合考慮各橡膠的耐熱性和“硫化返原”現象,各種橡膠建議的硫化溫度如下:
NR 在140-150℃,最高不超過160℃;
順丁橡膠、異戊橡膠和氯丁橡膠在150-160℃,最高不超過170℃
丁苯橡膠、丁腈橡膠可采用150℃以上,但最高不超過190℃;
丁基橡膠、三元乙丙橡膠一般選用160-180℃,最高不超過200℃;
硅橡膠、氟橡膠一般采用二段加硫,一段溫度可選170-180℃,二段硫化則選用200-230℃,按工藝要求可在4-24h 范圍內選擇。
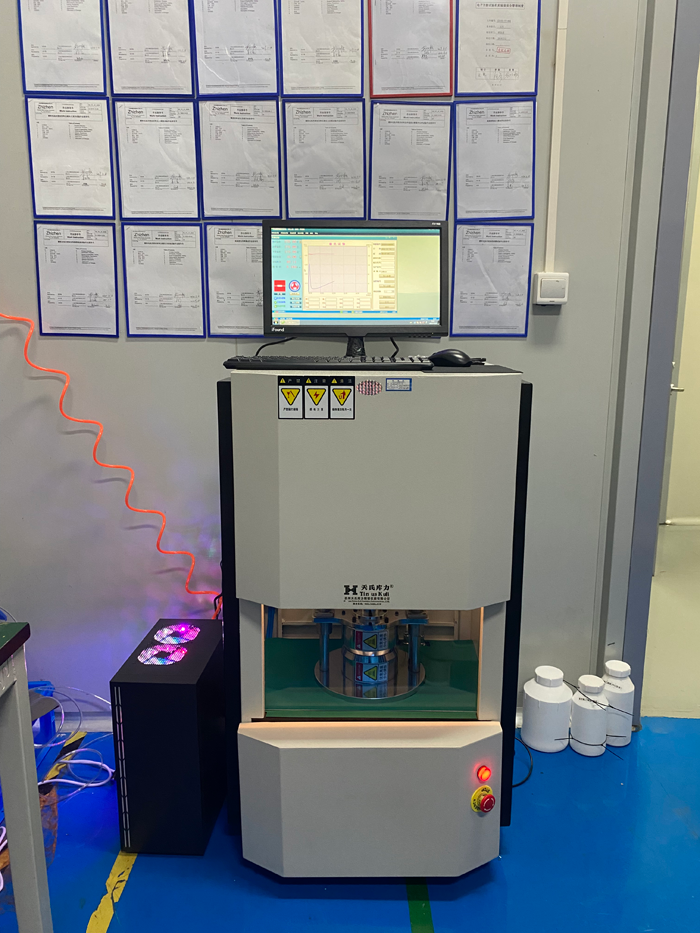
橡膠無轉子硫化儀示意圖
2.2 橡膠配方中硫化體系的類型
按照最終制品不同性能的要求,橡膠配方選用不同的硫化體系。硫化體系不同,則硫化特性不同,有的需要高活化溫度,有的需要低活化溫度。因此要根據實際的硫化體系來選擇相應的硫化溫度。通常,普通硫磺硫化體系,其硫化溫度選取范圍為130-160℃,具體需要根據所使用的促進劑的活性溫度和制品的物理機械性能來確定。
促進劑的活性溫度較低或制品要求高強度、較低的定伸應力和硬度時,硫化溫度可選擇較低一些,這樣生成較多的多硫交聯鍵;
促進劑的活性溫度較高或制品要求高定伸應力和硬度、較低伸長率時,硫化溫度宜采用高一些,這樣生成較多的低硫交聯鍵。
有效、半有效硫化體系,硫化溫度一般掌握在160-165℃之間,過氧化物及樹脂等非硫磺硫化體系,硫化溫度適合選擇170-180℃.尤其要指出,對于EPDM,NBR硫磺硫化的配方,如設計需要二次加硫,一次加硫與二次加硫的溫度和時間影響最終制品的壓縮*變形和硬度等機械性能均比較大;而過氧化物硫化的配方,一次加硫的溫度尤為重要,*在180℃以上,若一次加硫溫度不足,二次加硫補足的效果甚低。即過氧化物硫化的配方,二次加硫對最終物性的影響很小。
橡膠屬于熱的不良導體,受熱升溫較慢。對于厚制品來說,采用高溫硫化很難使內外層膠料同時達到平坦范圍;造成制品外表部分恰好正硫化時,而內部出現欠硫化?;蛘邇炔壳『贸霈F正硫化時,而外部已過硫化。為了保證厚制品硫化均勻,除了配方設計時需要充分考慮膠料的硫化平坦性外,在選擇硫化溫度時,也要考慮硫化溫度低一些或采用逐步升溫的操作方法。
l對于薄制品,硫化溫度可以適當高點。
對于夾織物的橡膠制品,通常硫化溫度不高于140℃.而發泡橡膠,需要按照發泡劑和發泡助劑的分解溫度選擇適宜的硫化溫度。
什么叫橡膠制品硫化時間?如何設定硫化時間?
1. 定義
1.1 橡膠制品硫化時間
站在一定的溫度、模壓下,為了使膠料從塑性變成彈性,且達到交聯密度最大化,物理機械性能化所用的時間叫橡膠制品硫化時間。通常不含操作過程的輔助時間。
硫化時間是和硫化溫度密切相關的,在硫化過程中,硫化膠的各項物理、力學性能達到或接近*點時,此種硫化程度稱為正硫化或最宜硫化。在一定溫度下達到正硫化所需的硫化時間稱為正硫化時間,一定的硫化溫度對應有一定的正硫化時間。當膠料配方和硫化溫度一定時,硫化時間決定硫化程度,不同大小和壁厚的橡膠制品通過控制硫化時間來控制硫化程度,通常制品的尺寸越大或越厚,所需硫化的時間越長。
2. 硫化時間的設定方法
2.1 正硫化時間的測試
膠料正硫化時間的測試方法有:
2.1.1物理-化學法(包括游離硫測定法和溶脹法);
2.1.2 物理-力學性能測定法(包括定伸應力法、拉伸強度法、定伸強度法、抗張積法、壓縮*變形法、綜合取值法等);
2.1.3儀器法(包括門尼粘度法、硫化儀法)等。
目前最常用的是硫化儀法。通過硫化儀測試,可以得到膠料的正硫化時間。
2.2 制品硫化時間的確定
2.2.1 若制品厚度為6mm或小于6mm,并且,膠料的成形工藝條件可以認為是均勻受熱狀態,那么,制品的硫化時間與硫化曲線中所測得的正硫化時間相同(溫度一致的情況下,即加硫溫度使用硫化儀測試的溫度);
2.2.2 若制品壁厚大于6mm,每增加1mm的厚度,則測試的正硫化時間增加1min,這是一個經驗數據。例如,一橡膠制品,其厚度為22mm,試片測試的正硫化時間為6min(溫度設定為150℃),那么,在150℃硫化時,該制品的硫化時間為6+(22-6)×1=22min。這時間不包括操作過程的輔助時間。
3. 二段加硫時間設定
3.1 定義為了達到合理的制造工藝和合理成本,把橡膠硫化分為一段、二段兩個過程來完成的工藝方法,其第二段的工藝就是所謂的二段加硫。一段硫化主要是使制品得到定形,然后將未100%正硫化狀態而得到定形的制品集中起來進行二段硫化。這樣,提升了一段硫化的效率,二段硫化的集中處理,也提升了效率,節省了能源。
3.2 二段硫化時間的設定
除合理成本考量,對于特種橡膠如Silicone膠、FKM橡膠,其正硫化過程的時間較長,正常工藝均采用二段硫化。
NR,一般不采用二段加硫。因其非常容易產生硫化返原現象。如需要建議在100℃以內,2小時左右;
SBR,BR一般采用100-120℃,1-2小時;
NBR,EPDM(硫磺硫化)一般采用140-150℃ 2-4小時;
EPDM (過氧)一般采用150-160℃ 2-4小時;
FKM一般采用 200-230 8-12小時。
推薦閱讀
【本文標簽】:硫化,儀測,得的,曲線,怎么,看,無,轉子,硫化,儀,測定,
【責任編輯】:天氏庫力 版權所有:http://www.jnshuntai.com/轉載請注明出處